Input Power
|
-
Single phase 220 VAC, 50 / 60 Hz
-
1000 W (including vacuum pump and water chiller)
-
If the voltage is 110 V, a 1500 W transformer can be ordered at TMAX.
|
Power Source
|
-
13.5 MHz, 100 W RF generator with manual matching is included and connected to the sputtering heads
-
Continuous working time:
-
100W: ≤ 1 hour
-
80W: ≤ 1.5 hours
-
70W: ≤ 2 hours
-
60W: ≤ 4 hours
-
50W: ≤ 8 hours
-
Load range: 0 – 80 adjustable. Tuning range: -200j – 200j adjustable
-
The rotatable switch can activate one sputtering head at a time. Sputtering heads can be switched “in the plasma” (no breaking of vacuum and plasma during a multilayer process)
-
With a DC power supply, the coater can be easily modified into 1” DC sputtering sources for metallic film deposition, enabling three DC, one RF / two DC, and two RF / one DC sputtering head configurations (Bottom left picture. Please select from the Product Options)
-
Optional 300 W auto-match RF generator is available at extra cost
|
Magnetron Sputtering Head

|
-
Three 1" magnetron sputtering heads with water cooling jackets are included and inserted into quartz chamber via quick clamps
-
RF cable replacement can be purchased at TMAX
-
One manually operated shutter is built on the flange (See Pic #3)
-
One 10 L/min digitally controlled recirculating water chiller is included for cooling sputtering heads
-
|
Sputtering Target
|
-
Target size requirement: 1" diameter x 1/8" thickness max
-
Sputtering distance range: 50 – 80 mm adjustable
-
Sputtering angle range: 0 – 25° adjustable
-
1" diameter Cu target and Al2O3 target are included for demo testing
-
Various oxide 1” sputtering targets are available upon request at extra cost
-
For target bonding, 1 mm and 2 mm copper backing plates are included. Silver epoxy (Pic #1) and extra copper backing plates (Pic #2) can be ordered at TMAX
|
Vacuum Chamber

|
-
Vacuum chamber: 256 mm OD x 238 mm ID x 276 mm Height, made of high purity quartz
-
Sealing flange: 274 mm Dia. made of Aluminum with high-temperature silicone O-ring
-
Stainless steel shield cage is included for 100% shielding of RF radiation from the chamber
-
Max vacuum level: 1.0E-5 Torr with optional turbo pump and chamber baking
|
Sample Holder
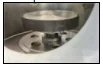
|
-
Sample holder is a rotatable and heatable stage made of ceramic heater with stainless steel cover
-
Sample holder size: 50 mm Dia. for. 2" wafer max (See picture below)
-
Rotation speed: 1 - 10 rpm adjustable for uniform coating
-
The holder temperature is adjustable from RT to 600 °C max (5 min max at 600 °C; 2 hr max at 500 °C) with accuracy +/- 1.0 °C via a digital temperature controller
|
Vacuum Pump
|
-
KF40 vacuum port is built in for connecting to a vacuum pump.
-
Vacuum level: 1.0E-2 Torr with included dual stage mechanical pump
-
1.0E-5 Torr with optional turbo pump
|
Optional
|
-
Precision quartz thickness sensor is optional. It can be built into the chamber to monitor coating thickness with accuracy 0.1 Å (water cooling required)
-
Easy USB connection to PC for remote thickness and coating speed monitoring
-
5 pcs quartz sensors (consumable) are included
-
Remote PC control of the temperature controller is optional
-
Easy USB connection to PC for remote temperature control
-
Temperature control software is included. The module is compatible with LabView
-
For DC magnetron sputtering, turbo pump is recommended (Pic #3)
-
Reactive sputtering with N2 or O2 is available with optional gas mixing control station.
-
|
Size
|
-
540 mm L x 540 mm W x 1000 mm H
|
Net Weight
|
|
Compliance
|
-
CE approval
-
MET Certification (UL 1450) is available upon request at extra cost, please contact our sales representative for quote.
|
Warranty
|
-
One years limited warranty with lifetime support
|
Application Notes
|
-
This compact 1" RF magnetron sputtering coater is designed for coating oxide thin films on oxide single crystal substrates, which usually does not need high vacuum set-up
-
A two-stage pressure regulator (not included) should be installed on the gas cylinder to limit the output pressure of gas to below 0.02 MPa for safe usage. Please use > 5N purity Ar gas for plasma sputtering
-
For the best film-substrate adhesion strength, please clean the substrate surface before coating:
-
Ultrasonic cleaning with the following sequential baths - (1) acetone, (2) isopropyl alcohol - to remove oil and grease. Blow dry the substrate with N2, then hot bake in vacuum to remove absorbed moisture
-
Plasma cleaning may be needed for surface roughening, surface chemical bonds activation, or additional contamination removal
-
A thin buffer layer (~5 nm), such as Cr, Ti, Mo, Ta, could be applied to improve adhesion of metals and alloys
-
For best performance, the non-conductive targets must be installed with a copper backing plate. Please refer to the instruction video below (#3) for target bonding
-
TMAX supplies single crystal substrate from A to Z
-
TMAX RF Plasma Sputtering Coaters have successfully coated ZnO on Al2O3 substrate at 500 °C (XRD profile in Pic #5)
-
Test the flexibility of the thin film/coated electrode with EQ-MBT-12-LD mandrel bending tester.
-
HIGH VOLTAGE! Sputtering heads connect to high voltage. For safety, the operator must shut down the RF generator before sample loading and target changing operations
-
DO NOT use tap water in water chiller. Use coolant, DI water, distilled water, or anti-corrosive additives with water
-
|